Key Takeaways
- Price Range: Expect to pay between $50,000 and $150,000 for new wrap-around case packers, depending on size, capacity, and features.
- Cost Factors: Type of case packer, production speed, material handling options, and custom features influence pricing.
- Lifespan & Maintenance: Wrap around case packers typically last 10–15 years with proper maintenance. Annual servicing can cost between $2,000–$10,000.
- Financing Options: Leasing, supplier financing, and equipment loans can help spread the cost of investment. Check for government grants in certain industries.
- Common Pitfalls: Overlooking the need for future upgrades, not considering production volume, or ignoring machine compatibility with existing systems.
Wrap around case packers are essential for packaging lines in industries like food and beverage, pharmaceuticals, and consumer goods. These machines efficiently wrap, seal, and pack products into cases, reducing manual labour and increasing throughput. This guide will help you understand pricing, key features, operational considerations, and maintenance to make an informed purchasing decision in 2025.
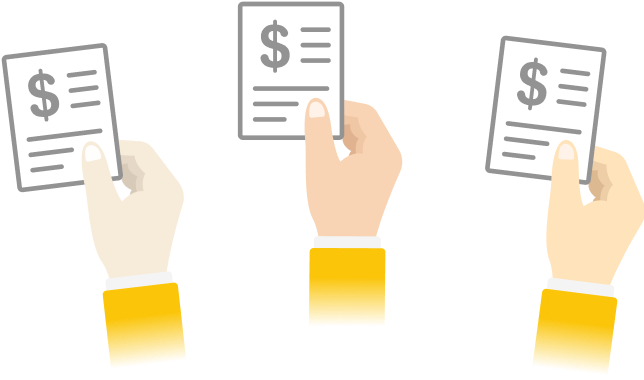
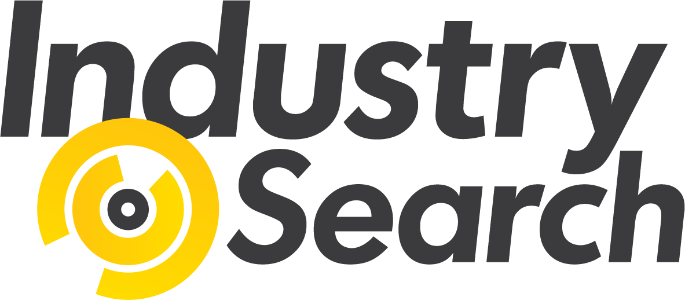
Find the right Wrap Around Case Packer
Compare quotes from expert Australian suppliers and make the best choice. It's free, quick and easy!
Understanding Pricing
Wrap around case packers come in a range of styles and configurations, each suited to different production needs. Here's a breakdown of pricing based on type and features:
Price Breakdown by Type
- Manual Wrap Around Case Packers: $50,000 – $70,000
- Semi-Automatic Wrap Around Case Packers: $70,000 – $100,000
- Fully Automatic Wrap Around Case Packers: $100,000 – $150,000
What Affects the Price?
- Type of Packer:
- Manual: Lower cost but requires more operator involvement.
- Semi-Automatic: Offers more automation but at a mid-range price point.
- Fully Automatic: Expensive but significantly reduces the need for human labour.
- Production Speed: Higher speed systems that can handle more cases per minute (CPM) will generally cost more. Average speeds range from 15–40 CPM, with top-end machines reaching up to 100 CPM.
- Material Handling Options: Integration with conveyors, automated loading, and product feeders can increase costs, but these upgrades boost efficiency.
- Custom Features: Customised machines designed to handle unique product shapes or sizes may cost more but offer better flexibility.
Key Features to Consider
1. Production Capacity
- Match the packer’s capacity to your production volume. Consider how many cases you need to pack per minute and whether the system is scalable for future growth.
2. Automation and Integration
- Automation: Fully automated machines require less manual labour, reducing overhead costs over time. This feature is crucial for large-scale operations.
- System Integration: Make sure the case packer integrates seamlessly with existing systems such as conveyors, product feeders, and palletising equipment.
3. Case Size Flexibility
- Look for models that can accommodate a range of case sizes. This flexibility is especially important for companies with diverse product lines.
4. Product Handling
- Ensure the packer can handle your specific product types—whether they’re fragile, heavy, or irregularly shaped.
5. Ease of Maintenance
- Choose a machine with easy-to-replace parts and minimal downtime for maintenance. Automated diagnostics are a great feature to help troubleshoot issues quickly.
Financing Options
The investment in a wrap-around case packer is significant, but several financing options can make the purchase more manageable:
- Leasing: Leasing allows businesses to spread the cost over time, with fixed monthly payments. It’s ideal if you prefer flexibility or if you anticipate needing upgrades in the near future.
- Supplier Financing: Some manufacturers offer in-house financing or payment plans, which could include service packages or extended warranties.
- Bank Loans: Many financial institutions offer loans specifically for machinery and equipment purchases, with flexible terms and competitive interest rates.
- Government Grants: In sectors such as food production, there may be government grants available that help subsidise machinery costs. Research programs specific to your industry.
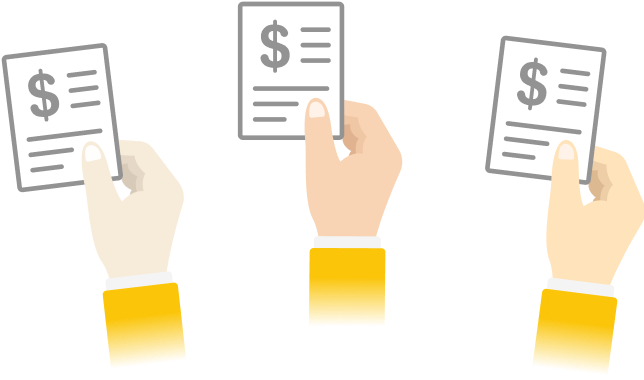
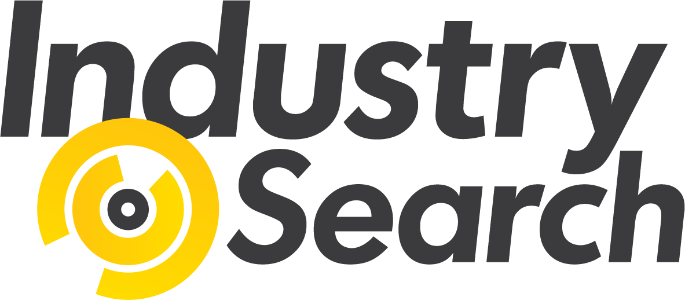
Find the right Wrap Around Case Packer
Compare quotes from expert Australian suppliers and make the best choice. It's free, quick and easy!
Parts & Warranties
Common Parts
- Conveyor Belts: Ensure that belts are made from durable, easy-to-clean materials, especially if you're packing food products.
- Sealing Mechanisms: The quality of the sealing system impacts the integrity of the packed cases.
- Sensors & Control Systems: Modern wrap-around case packers feature advanced sensors that detect product placement and adjust the packing process accordingly.
Warranties
- Standard Warranties: Typically range from 1 to 5 years. This covers most of the main parts, including the conveyor and motor systems.
- Extended Warranties: Some suppliers offer extended warranties for an additional cost. These may include routine servicing, technical support, and priority repair services.
- Annual Maintenance Plans: Annual servicing can cost $2,000 to $10,000, depending on the level of support and the complexity of the machine.
Operational Efficiency & Cost-Saving Tips
1. Optimising Throughput
- To maximise your investment in a wrap-around case packer, optimise throughput by selecting the right case material, adjusting speeds for peak production periods, and streamlining product handling processes. Choose case packers with features that can boost speed during high-demand times, such as adjustable speeds based on load size.
2. Reducing Downtime
- Minimise downtime by implementing a proactive maintenance schedule. Regular maintenance checks can help detect issues early, reducing the risk of unexpected breakdowns. Stock essential spare parts to avoid waiting for replacements.
3. Energy Efficiency
- Consider investing in energy-efficient models or machines with auto power-down features to reduce long-term energy costs. Some packers come with energy-saving settings that reduce electricity consumption during idle times.
Regulatory Compliance & Industry Standards
- Food Safety: For food packaging, ensure compliance with HACCP, FDA standards, and other health regulations. Select machines that meet these for safety, particularly when packing consumables.
- Material Handling: Adhere to product-specific material handling standards, like FDA-compliant seals and tamper-evident packaging, to maintain regulatory compliance.
Upgrades, Customisation & Future-Proofing
- Custom Features: If packing diverse or irregular products, choose packers with adjustable conveyors and specialised loading mechanisms for greater flexibility.
- Future-Proofing: Opt for modular systems that allow upgrades in speed and automation, ensuring scalability as production needs grow.
Common Buyer Questions
1. How do I know which size wrap around case packer I need?
- Match the packer’s capacity to your production volume. If your line produces 100 cases per minute, a system capable of handling 120–150 cases per minute would provide ample capacity for growth.
2. How often do I need to service a wrap-around case packer?
- Typically, servicing is recommended annually. However, some models may require more frequent maintenance, especially in high-volume environments.
3. Can I upgrade my wrap-around case packer in the future?
- Yes. Many models offer modular upgrades, such as increased speed or the addition of automated case handling features, to improve efficiency.
4. What’s the difference between manual, semi-automatic, and fully automatic models?
- Manual: Requires significant operator intervention.
- Semi-Automatic: Automates some functions, requiring fewer operators.
- Fully Automatic: Operates independently, with minimal human intervention, providing the highest efficiency.
5. How do I know if a wrap-around case packer is compatible with my product?
- Always check the product specifications of the packer to ensure it’s designed for your product type. This includes checking case sizes, product weight, and material compatibility.
Conclusion
Investing in a wrap-around case packer in 2025 can boost efficiency and streamline your production line. By understanding the key factors that influence pricing, automation, and maintenance, you can make an informed decision that aligns with your company’s needs. Whether you choose manual, semi-automatic, or fully automatic options, consider long-term serviceability, production speed, and integration with existing systems.