Industrial touch screen monitors have become integral components in modern manufacturing and process control environments.
They offer a user-friendly interface, intuitive controls, and real-time data visualization, enabling operators to interact seamlessly with complex industrial systems. However, to harness the full potential of industrial touch screen monitors, proper installation and calibration are essential.
This comprehensive guide delves into the best practices for installing and calibrating industrial touch screen monitors. From mounting and placement considerations to cable management, environmental protection, and seamless integration with control systems, we explore the critical steps to ensure optimal usability, accuracy, and reliability of industrial touch screen monitors in industrial settings.
1. Proper Mounting and Placement for Optimal Usability
The correct mounting and placement of industrial touch screen monitors is a critical factor that significantly impacts the overall usability and efficiency of these essential tools in manufacturing and industrial settings. Properly positioning touch screen monitors not only enhances the user experience but also contributes to improved productivity, reduced operator fatigue, and minimized errors.
Here are the key aspects of mounting and placement, highlighting their significance in optimizing the functionality and effectiveness of industrial touch screen monitors.
-
Ergonomic Considerations for Operator Comfort:
One of the primary reasons why proper mounting and placement are essential is to ensure operator comfort and ergonomics. Industrial touch screen monitors are frequently used by operators for extended periods. Therefore, placing the monitors at an ergonomic height and angle is crucial to reducing operator strain and discomfort during prolonged usage. An ergonomic setup minimizes the risk of musculoskeletal issues and promotes a healthier working environment, ultimately leading to increased operator satisfaction and improved overall efficiency.
-
Visibility and Line of Sight:
Another crucial aspect of mounting and placement is to ensure a clear line of sight for operators. Placing the industrial touch screen monitor at a location where operators have an unobstructed view of the entire screen content is vital. Avoiding installation behind equipment or obstacles that could block the display ensures that operators can access information and control functions without hindrance. Unobstructed visibility also helps operators monitor processes more effectively and respond to critical events promptly, thereby enhancing overall operational efficiency.
-
Avoiding Glare and Reflections
Mounting industrial touch screen monitors in a way that minimizes glare and reflections is of paramount importance. Direct sunlight or bright lights shining on the screen can cause distracting reflections, making it challenging for operators to read the display. Glare can also cause eye strain and reduce visibility, leading to potential errors in operating machinery or monitoring processes. Proper placement to avoid direct sunlight and positioning away from reflective surfaces significantly improves screen readability and contributes to a more productive work environment.
-
Stability and Resistance to Vibration
Industrial environments often involve machinery and equipment that generate vibrations. Proper mounting solutions that ensure stability and resistance to vibration are crucial for industrial touch screen monitors. Securely mounting the monitors prevents them from shaking or moving during operation, ensuring consistent touch accuracy and preventing accidental touches. Stable mounting also prolongs the lifespan of industrial touch screen monitors by reducing the wear and tear associated with constant movement.
-
Choosing the Right Touch Screen Size
Selecting an appropriate touch screen size based on the specific application and viewing distance is essential. Larger screens may be more suitable for applications where operators need to access multiple data points simultaneously, while smaller screens may be sufficient for applications with limited data visibility requirements. The right touch screen size ensures that operators can interact with the interface comfortably and efficiently, promoting faster task completion and improved overall productivity.
-
Considering Touch Screen Type and Technology
Industrial touch screen monitors come in various types and technologies, such as resistive, capacitive, or infrared. The choice of touch screen technology can influence placement considerations. For example, capacitive touch screens are highly responsive and do not require physical pressure, making them ideal for applications where operators need to wear gloves. Considering the specific industrial touch screen technology and its suitability for the intended application helps optimize placement for the best user experience.
-
Accessibility and Reachability
The industrial touch screen monitor should be easily accessible and reachable for operators. Placing the monitor within easy reach ensures that operators can comfortably interact with the interface without straining or stretching. Easy accessibility reduces operator movement, allowing for more efficient multitasking and reducing the risk of accidental touches or errors caused by reaching too far.
-
Adapting to Specific Application Requirements
The mounting and placement of industrial touch screen monitors should be tailored to the specific application and workflow. Different industrial processes may have unique requirements in terms of touch screen placement. For instance, industrial touch screen monitors in control rooms may require wall-mounted or console-mounted configurations for optimal operator convenience, while industrial touch screens on manufacturing equipment may require integration into the machine's control panel for seamless operation.
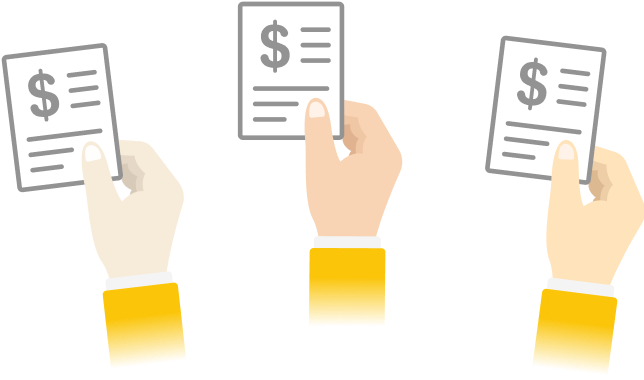
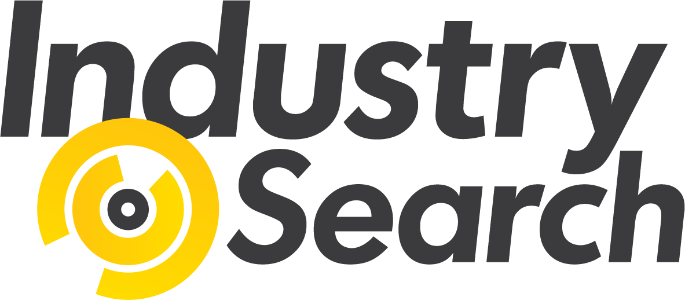
Find the right Industrial Touch Screen Monitor
Compare quotes from expert Australian suppliers and make the best choice. It's free, quick and easy!
2. Calibrating Touch Screen Accuracy: Ensuring Precise Inputs
Calibration is an indispensable and intricate process that plays a pivotal role in guaranteeing the utmost accuracy and responsiveness of touch screen inputs. By meticulously calibrating the industrial touch screen monitor, operators can be assured that their touch interactions align precisely with the displayed content. This meticulous alignment eliminates any discrepancies or misalignment between the user's touch and the corresponding on-screen response, ensuring a seamless and intuitive user experience.
During calibration, the industrial touch screen monitor is calibrated at multiple points across its surface, establishing a reference framework for touch inputs. Each touch point is meticulously mapped and calibrated to accurately correspond with the display's visual elements. By calibrating at multiple points, the touch screen monitor accounts for any potential variations in touch sensitivity, environmental factors, or manufacturing tolerances, thus providing a consistent and accurate touch experience across the entire screen.
Consider the following steps:
Calibration Tools: Utilize manufacturer-provided calibration tools or third-party software to perform accurate touch screen calibration. These tools guide operators through the calibration process, adjusting touch sensitivity and accuracy.
- Multi-Point Calibration: Perform multi-point calibration to improve accuracy across the entire touch screen surface. Multi-point calibration establishes touch reference points for different areas of the display, ensuring consistent accuracy across the entire screen.
- Regular Calibration Checks: Regularly check and recalibrate touch screen monitors to maintain accuracy over time. Factors like temperature variations and wear can affect calibration, necessitating periodic checks and adjustments.
- Operator Feedback: Involve operators in the calibration process and gather their feedback on touch screen responsiveness. Operator feedback can help fine-tune calibration settings for improved usability.
- Factory Calibration vs. On-Site Calibration: Some industrial touch screen monitors come with factory calibration, while others require on-site calibration. Follow manufacturer guidelines and best practices for both types of calibration.
3. Cable Management and Protection: Preventing Damage and Downtime
Proper cable management and protection are crucial to ensure the longevity and reliability of industrial touch screen monitors in industrial environments. Consider the following best practices:
- Secure Cable Routing: Securely route cables to prevent them from getting entangled or obstructing the touch screen's movement. Use cable ties and cable management accessories to keep cables organized.
- Protect Cables from Abrasion: In industrial settings with moving machinery or sharp edges, use cable protectors or conduit to shield cables from abrasion and potential damage.
- Avoid Tight Bends: Avoid tight bends or kinks in cables, as they can cause signal interference and affect touch screen performance. Maintain proper bend radius for cable longevity.
- Use Industrial-Grade Cables: Opt for industrial-grade cables that are designed to withstand harsh environmental conditions and offer enhanced durability.
- Seal Cable Entry Points: Ensure cable entry points on the industrial touch screen monitor are properly sealed to prevent dust, debris, and moisture from entering the enclosure.
4. Environmental Protection: Sealing Touch Screen Monitors against Harsh Elements:
Industrial environments can expose industrial touch screen monitors to various harsh elements, including dust, moisture, and chemicals. Proper environmental protection is essential to ensure the reliable and long-lasting performance of industrial touch screen monitors. Consider the following measures:
- IP Rating: Choose industrial touch screen monitors with a suitable IP (Ingress Protection) rating that corresponds to the environmental conditions in which they will be used. Higher IP ratings indicate better protection against dust and moisture ingress.
- NEMA Rating: In North America, NEMA (National Electrical Manufacturers Association) ratings provide similar information to IP ratings. Select industrial touch screen monitors with appropriate NEMA ratings for specific environmental challenges.
- Sealed Enclosures: Ensure that the industrial touch screen monitor's enclosure is properly sealed to prevent the entry of dust, moisture, and other contaminants. Gaskets, seals, and adhesives may be used to achieve a robust seal.
- Chemical Resistance: In environments where industrial touch screen monitors may come into contact with chemicals or cleaning agents, opt for monitors with chemical-resistant coatings or materials.
- Temperature and Humidity Considerations: Ensure that industrial touch screen monitors can operate reliably within the specified temperature and humidity ranges of the industrial environment.
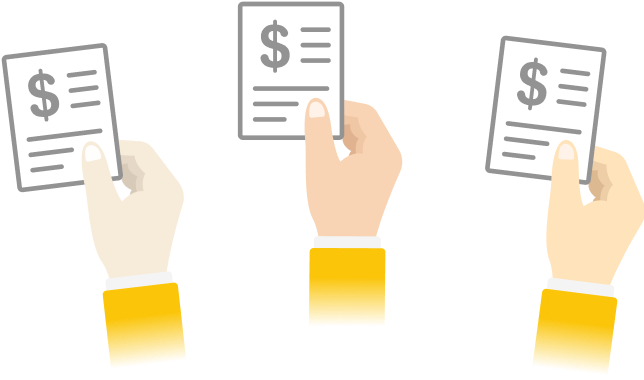
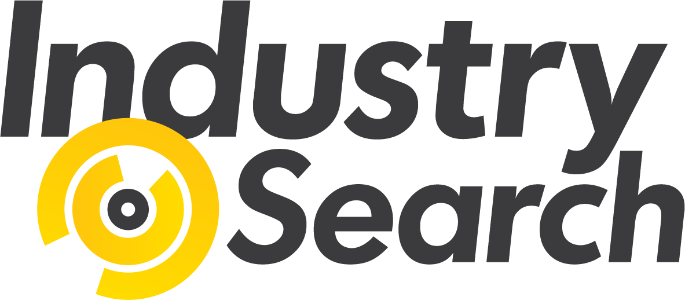
Find the right Industrial Touch Screen Monitor
Compare quotes from expert Australian suppliers and make the best choice. It's free, quick and easy!
5. Seamless Integration with Industrial Control Systems (PLCs, SCADA, etc.):
For efficient industrial operations, industrial touch screen monitors must seamlessly integrate with existing control systems, such as Programmable Logic Controllers (PLCs) and Supervisory Control and Data Acquisition (SCADA) systems. Consider the following integration aspects:
- Communication Protocols: Ensure that the industrial touch screen monitor supports the communication protocols used by the industrial control system. Common protocols include Modbus, Profibus, Ethernet/IP, and DeviceNet.
- HMI Software Compatibility: Verify that the industrial touch screen monitor's Human-Machine Interface (HMI) software is compatible with the control system's software. Compatibility ensures smooth data exchange and seamless visualization of process parameters.
- Data Mapping and Tagging: Properly map and tag data points between the industrial touch screen monitor and the control system for accurate data exchange and synchronization.
- Real-Time Data Visualization: The industrial touch screen monitor should provide real-time data visualization and enable operators to monitor critical process parameters and alarms effectively.
- Alarm Management: Ensure that the touch screen monitor can display and manage alarms from the control system, enabling operators to respond promptly to critical events.
6. Rigorous Testing and Quality Assurance for Reliable Performance
Before deploying industrial touch screen monitors in industrial environments, rigorous testing and quality assurance are essential to ensure reliable performance. Consider the following testing procedures:
- Functional Testing: Conduct functional testing to verify that all touch screen features and functionalities are working correctly. This includes testing touch sensitivity, multi-touch gestures, and on-screen controls.
- Temperature and Environmental Testing: Subject industrial touch screen monitors to temperature and environmental tests to validate their performance under the expected operating conditions.
- Vibration and Shock Testing: Test industrial touch screen monitors for resistance to vibration and shock to ensure their reliability in industrial environments with mechanical equipment.
- Durability Testing: Conduct durability tests to assess the industrial touch screen monitor's ability to withstand physical impacts and harsh handling.
- Calibration Verification: Verify touch screen calibration accuracy after installation to ensure precise touch inputs.
Proper installation and calibration of industrial touch screen monitors are pivotal for optimizing usability, accuracy, and reliability in manufacturing and process control environments. Mounting the monitors ergonomically, calibrating touch accuracy, managing and protecting cables, ensuring environmental protection, seamless integration with control systems, and rigorous testing all contribute to the efficient and effective performance of touch screen monitors. By following these best practices, industrial professionals can maximize the value of touch screen technology and leverage its transformative potential to enhance productivity and streamline operations in their industrial processes. With a thorough understanding of the installation and calibration process, industries can unlock the full benefits of touch screen monitors and pave the way for a more connected, efficient, and productive industrial landscape.